
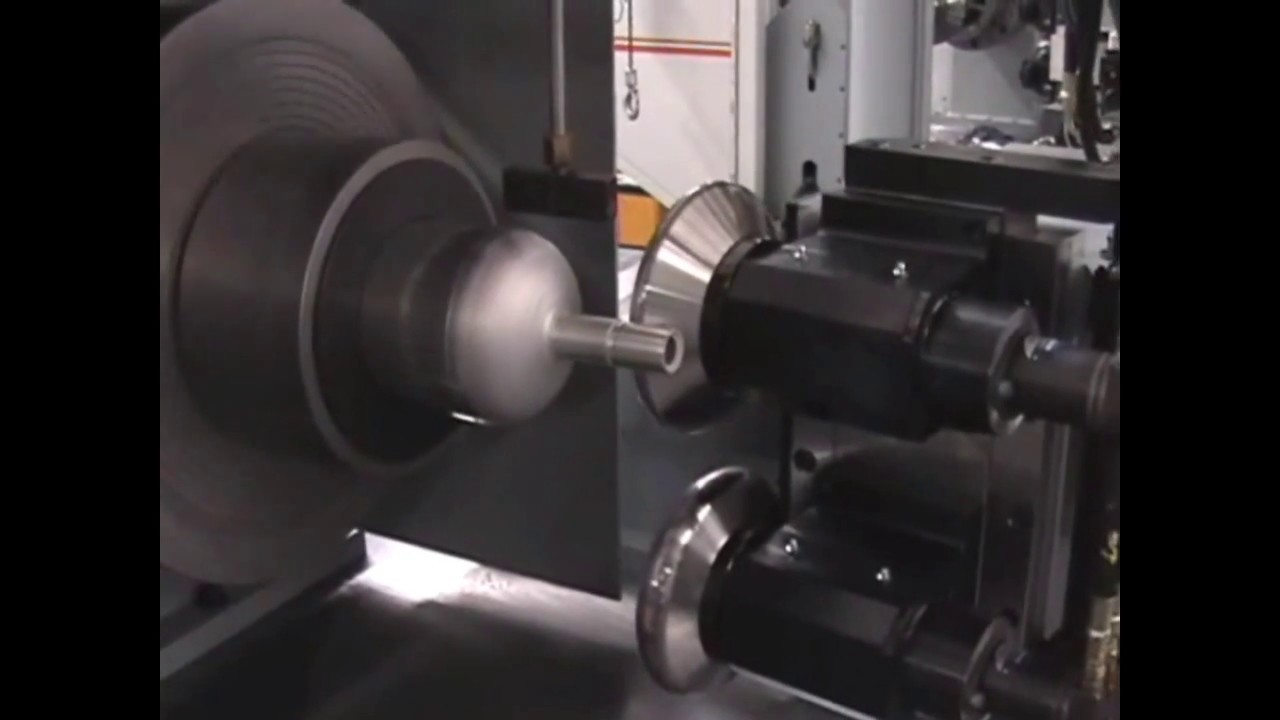
The end product can have practically any arrangement the designer wants.įurthermore, the reluctance to working challenges can be improved, directional attributes can be managed, and a pleasing look can be developed. Thus, in just one step, complex or simple shapes can be crafted from any kind of metal that has the capability to be melted. – Heat treatment must be applied afterwards.Ĭasting is a manufacturing process in which a solid is dissolved into a liquid, heated to appropriate temperature (sometimes processed to change its chemical formula), and is then added into a mold or cavity. Repetitive manufacturing is used for repeated production that is committed to a specific production rate. The metal press such as die and punching tools are implemented for this manufacturing process.Īdvantages: – Same equipment can be utilized for manufacturing various components by simply changing the dies.ĭisadvantages: – High apparatus and tooling expenses. Bending, spinning, drawing, and stretching are a few important metal forming process in manufacturing. Metal forming is the approach of creating the metallic components by deforming the metal but not by removing, cutting, shredding or breaking any part. Welding also can minimize costs related to extra parts, for example angles mounted between parts. Fasteners don't have to be purchased and stored in stock. It doesn't require overlapping materials, and so it removes excess weight brought on by other fastening methods. Welding is generally a cost-effective approach to fabricate. However, all joint patterns must consider features such as load factors, assembly effectiveness, operating surroundings, overhaul and upkeep, and the materials chosen. Naturally, joints intended for the two approaches would differ tremendously.
Design for assembly, and fastener selection apply their own specifications.īolting is a standard fastening method, for instance, but welding may cut down the weight of assemblies. Figure 3: The field of research presented in the thesis together with area of contribution for the appended papers. Non-traditional machine tools implement light, electric powered, chemical, and sonic power superheated gas and high-energy compound beams to form the exotic supplies and materials that have been created to meet the requirements of modern technology.Įvery joining approach has particular design needs, while certain joint needs may propose a particular joining approach. Presses implement a several shaping processes, which includes shearing, pressing, or elongating. Traditional chip-making tools form the work-piece by trimming away the unwanted part accessible as chips. They are categorized under three main categories: Machine tools make up the foundation of advanced industry and are utilized either indirectly or directly in the manufacturing of tool parts. The forming is done by removing extra materials from a work-piece. Tools used for machining are immobile power-driven units used to form or shape solid materials, specifically metals. Below are some of the manufacturing processes that are worth reading.įollowing are the 4 types of manufacturing processes It also explains and illustrates the use of several hand tools (calibrating, marking, forming and supporting gear etc.), tools, machinery and diverse methods of production that facilitate forming or shaping the existing raw materials into appropriate usable forms. It deals with numerous aspects of workshops procedures also for providing the basic working awareness of the various engineering materials, tools, accessories, manufacturing processes, basic concepts of machine instruments, production criteria’s, traits and uses of numerous testing instruments and calibrating or inspecting units for checking materials or products designed in various production shops in a commercial environment. The complete knowledge of fundamental workshop technology and manufacturing processes is highly troublesome for anybody to claim competence over it. Beside above, all the future technicians must understand the basic needs of workshop routines in terms of man, equipment, material, methods, revenue and other infrastructure conveniences needed to be placed properly for maximum shop or plant layouts and other support solutions effectively regulated or positioned in the field or industry within a properly planned manufacturing firm.
